As mentioned previously, the suspension design (and, to a large extent, the rest of the car design) has been finalised and the SUFST build process has started. However, finalising the design is more than a case of finishing a part and printing out a drawing, as every part needs to go through an extensive validation procedure.
Geometry Validation
The geometry has been fixed for a couple of months, as it needs to be finalised very early on to allow for chassis and bodywork development. We have continued to evaluate this geometry and check that it will behave as we expect.
This means using a variety of models and calculations to simulate, or at least attempt to characterise, the vehicle handling. There are many checks that we have to get through in order to be sure that the geometry is not going to be a problem, some of which have been derived from problems that we have experienced in previous years.
Firstly, we check that at full travel of the steering left-right, and full travel of the suspension in jounce and rebound, that none of our linkages will lock out or invert. We discovered in the course of this test that the steering would rotate (theoretically) more than 90 degrees before the steering rack locked out, and this necessitated a change to the steering pickup point.

We also check that the variation of wheel angles and offsets is not too severe in the course of the suspension travel. Last year, the car experienced a significant amount of dynamic toe – the rear wheels were trying to turn outwards as the suspension was compressed. We investigated the cause of the problem and engineered in a solution from the start this year, but we still needed to check that everything was under control. Camber angles should never go positive on loaded wheels, so this has been checked, as have the tyre scrub offsets, because they will contribute to steering feel and tyre wear.
The validation takes place using a number of different systems, including our dynamic model, Adams, and Microsoft Excel, with each one cross-checking the results of the others to make sure there is agreement.

Mating and Assemblies
The majority of the parts in the suspension system were designed in CAD in time for the December design deadline, which allowed for validation to take place over Christmas. Designing the parts in CAD is a long and frustrating exercise, because in order to define the geometry properly, almost all of the dimensions which can be used to sensibly define the part are not round numbers.
If we want to play with the design at a later date, for example to check for clashes as the corner travels, the parts need to be of an exact design. The best way to check for clashes is to physically drag the model, so the model needs to be mated realistically. The dimensions will have to match exactly, otherwise the assembly will not build properly.
This leads to a novel way of designing all of our parts. We build all of the parts around the wireframe sketch used to generate the geometry, which means that we take references off points in this sketch. The references that we use are therefore identical between components, and the parts are designed in car space to make the assembly easier. Once the part has been fully designed and specified, it can be dropped into the corner assembly and we can be sure that all of the parts will mate realistically.
The suspension assemblies are mated entirely by the mechanical linkages which defined them. This represents four point mates at the centre of the spherical bearings on the chassis end of the wishbones, and two point mates at the upright end. The push rod is also a point mate at both ends, and the rocker chassis mount is a concentric mate to ensure that rotation occurs around the correct axis. Within the upright assembly, the clevises are mounted to the uprights by two bolts, and the bearing and axle are accurately represented.
These mates to define the suspension will allow the system to still rotate around its steering axis, because the steering system is defined separately. There is therefore an additional mate to define the steering angle.
The steering and suspension systems have very similar geometry sketches, and these are linked together so that the references are maintained between the systems and we can be sure that the steering linkages will all be the right length once the model and the car are assembled.
Access to Parts
Once the CAD has been fully built, we need to check that it is physically possible to assemble all of the parts in the suspension system. This means checking that there is access for tools to bolt heads, enough space around the nuts to get a spanner on, and that the installation is not through a gap which the part will never pass through in the first place. All of these are problems that we have encountered before.
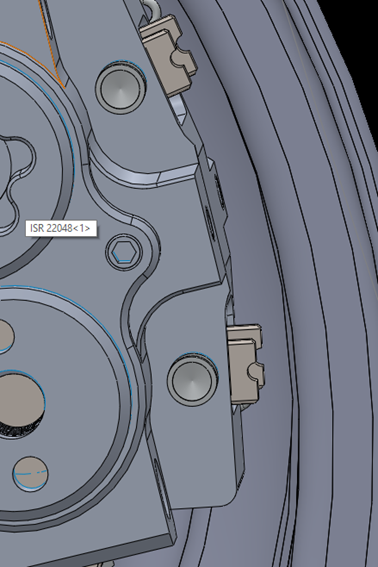
This is a very important part of the design validation which is often overlooked, because the CAD makes it very easy to assemble up a design without really considering how it will be manufactured or assembled. If there is a fundamental lack of access to a critical fastener, it can force a whole redesign of a particular subsystem, which is time consuming and very expensive.
A visual check is used to confirm that there is plenty of clearance for most of the parts, although in some cases we need to measure the component or try to drag it out without clashing to make sure that it is possible. A great way to visualise the assembly is to put together an exploded view, as this will show how the parts need to be assembled. It will reveal any possible clashes in the system.
This applies to more than just the suspension system too. For both structural and aerodynamic reasons, the chassis is wrapped as tightly around the engine as possible. This can present challenges when manoeuvring the engine into and out of the car – so checking that the engine can be moved in to its mounting points without clashing is very important.
We checked this by defining a path which the engine could move along in order to reach its mounting points, then dragging the engine step by step along this path, checking for contact at each stage. This method showed clearly the way in which the engine would have to be handled in order to get it into the car, and allowed us to plan for this installation in advance.
Finite Element Analysis
One of the last steps taken in the validation process is a full finite-element structural analysis of the part. This will model the potential stresses and deflections at each point in the part. The design has been done in conjunction with lower resolution scans, but now the higher detail scans can be completed with a better accuracy and faster processing.

The FEA which we complete on our parts gives us an idea of the potential effects of lack of rigidity in the system. We will be able to predict any deflection in wishbones, uprights, and linkages, and see if they are significant in controlling the vehicle dynamics.
This is an important step – one which is often overlooked and which can cause huge problems if a small amount of deflection reduces a small tolerance to an interference. For us, the location of the brake discs about 3mm away from a bolt head is a concern, because although the nominal dimension is 3mm, manufacturing tolerances have the potential to reduce this to 1.5mm. Add in the 0.5mm deflection which we could see on the brake disc, and the spacing is suddenly more of a concern. In this case, even in the worst case scenario there is no clash, but it could easily have been closer than this if the design had been done slightly differently.
FEA Setup
Making sure that the parts are strong enough to withstand the loads required is important, but what loads should actually be applied to the parts? In parts which are buried deep within other assemblies or connected to highly dynamic components, predicting the loads is not easy. We use our dynamic models and a little intuition to choose load cases which will prove that the part is strong enough in the relevant directions, without doing any tests which are irrelevant and may lead to adding weight that does not need to be there.

We can also expand the test to include more components, and use contact constraints to specify how the loads will be transferred through the parts. This is, in reality, the only way to properly test the suspension setup because so many of the connections are bearings or bolts with particular ways of transferring load.
The problem with this is that contact constraints are very computationally expensive to resolve, and the simulations take a very long time to run. They can often fail to converge, which is very annoying if the simulation has been running for 24 hours or more. As a result, the decision is often taken to make acceptable simplifications and add a safety factor to the result.
Our suspension has been designed to withstand 1g longitudinal, 2g lateral, and 3g bump at the contact patch (at the same time – worst case scenario). On top of this, there is a 1.5 load factor on any inputs used in the system, so that we can be confident the parts we are using are adequate. We use our models to determine the loads in each suspension member and then evaluate the loads in clevises, uprights, and hubs using free body diagrams from the known wishbone loads. We have found this to be an effective way of estimating representative forces.
Safety Factors
The most common way of dealing with any potential errors in simulations is to add a safety factor to the result. However, due to the dynamic and non-linear nature of some of the suspension behaviour, we choose to apply load factors to the input instead. This means scaling up the expected loads by 1.5-2 so that we can be confident that any shock loads can be dissipated safely.
The method of adding load factors means that if there are non-linearities in the system, such as excess deflection causing yielding, or deformation of springs into bump rubbers, they will be identified more easily than by checking for safety factors afterwards.
Load factors are the best way to properly check that the system can withstand the required loads. Of course, physical testing then has to take place to ensure that the software predictions match actual load conditions, and this leads to very enjoyable sessions trying to break pieces of carbon tube and metal inserts.
Manufacture
Even after the manufacturing stage has started there will still be some validation to complete. We can employ non-destructive testing techniques to check the strength of every part before they go on the car, and we can check the access and travel available in subassemblies before they are built on to the car.
We can make jigs and templates which will confirm that parts have been manufactured correctly before we start assembling them on to the car. This can include using other parts to check – we can assemble the chassis tabs with the wishbones attached so that we know they will slot on when required. We can repeat this process with any other tabs which need to be attached to the chassis, or with our wing attachment points.
The aim is to make the manufacturing and build run as smoothly as possible and produce a car which has no inherent issues once it is finished. This is an ambitious goal, but we are getting closer every year.
The build phase should continue through the Easter break before we start testing during the summer term.